Building a production line for concrete blocks is more than just laying out machinery; it’s about creating a system that ensures efficiency, quality, and long-term profitability. Whether you’re an entrepreneur stepping into the construction industry or a seasoned professional looking to upgrade, a well-organized production line is the backbone of success.
Concrete blocks are in high demand across residential, commercial, and industrial construction projects. With urbanization and infrastructure development on the rise, the need for reliable, cost-effective building materials has never been greater. By setting up an efficient production line, you can tap into this growing market while maintaining quality and minimizing costs.
This guide will walk you through the essentials of setting up a concrete block production line. From choosing the right location to selecting machinery and streamlining operations, every step is crucial. Let’s explore how you can lay the foundation for a profitable and sustainable business.
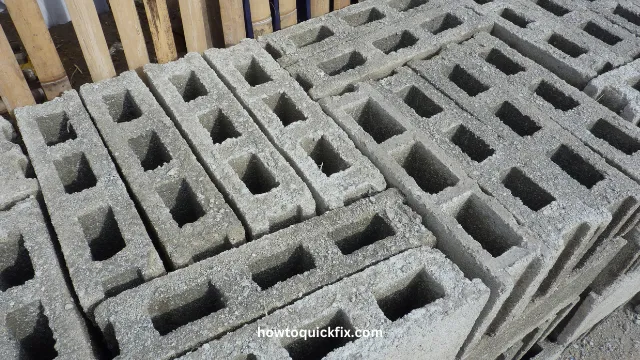
Contents
- 1 1. Selecting the Right Location
- 2 2. Procuring the Necessary Machinery
- 3 3. Ensuring Quality Control
- 4 4. Streamlining Workflow
- 5 5. Sustainability and Waste Management
- 6 Conclusion
- 7 FAQs
- 7.1 What machinery is essential for a concrete block production line?
- 7.2 How much space is required for setting up a production line?
- 7.3 Can I automate my concrete block production line?
- 7.4 What raw materials are needed for concrete blocks?
- 7.5 How can I ensure sustainability in production?
- 7.6 Is it necessary to test blocks for quality?
1. Selecting the Right Location
The location of your production line plays a critical role in its success. A centralized location reduces transportation costs and ensures accessibility for raw materials and delivery.
Ensure the site has adequate space for storage, machinery, and vehicle movement. Proximity to markets can significantly lower logistical expenses and improve customer satisfaction.
Consider local zoning laws and environmental regulations to avoid legal complications. A strategically chosen site sets the foundation for a smooth production process.
2. Procuring the Necessary Machinery
Investing in high-quality machinery is essential for consistent and efficient production. Start by identifying the type of blocks you want to produce, such as solid, hollow, or interlocking blocks.
Machines like concrete mixers, block-making machines, and curing systems are vital. Automated machinery, while more expensive upfront, can increase productivity and reduce labor costs.
Don’t forget about maintenance and repair services. Reliable machinery ensures minimal downtime, keeping your production line running efficiently.
3. Ensuring Quality Control
Quality is the cornerstone of a successful production line. Develop a system to monitor the mixing ratio of cement, sand, and water to ensure consistency.
Regular testing of blocks for strength and durability is crucial to meet industry standards. Implementing quality control measures early on builds customer trust and minimizes rework.
Train your staff to handle machinery and inspect products effectively. A well-trained team is key to maintaining high-quality output.
4. Streamlining Workflow
A well-organized workflow enhances productivity and reduces waste. Arrange machinery and workstations in a logical sequence to avoid bottlenecks.
Implement a conveyor system to transport materials efficiently. This reduces manual labor and speeds up production.
Use software to manage inventory, monitor production, and forecast demand. Automation tools can significantly improve your operational efficiency.
5. Sustainability and Waste Management
Sustainability is not just a trend; it’s a necessity in today’s business environment. Use eco-friendly raw materials, such as fly ash or recycled aggregates, to minimize your environmental impact.
Implement a waste management system to recycle leftover materials. This not only saves costs but also enhances your brand’s reputation.
Consider energy-efficient machinery to reduce power consumption. A sustainable production line attracts environmentally conscious clients and boosts profitability.
Conclusion
Setting up a production line for concrete blocks is a multi-faceted process that requires careful planning and execution. From selecting the perfect location to investing in reliable machinery and maintaining high-quality standards, every decision impacts your success.
By streamlining workflows and embracing sustainability, you can build a production line that is not only efficient but also future-proof. Remember, this is more than just an industrial setup—it’s an opportunity to meet growing market demands and contribute to the construction industry’s progress.
As you embark on this journey, stay focused on your goals and adapt to changes. A well-designed production line is the foundation for a thriving business in the competitive world of concrete blocks.
FAQs
What machinery is essential for a concrete block production line?
You’ll need concrete mixers, block-making machines, curing systems, and conveyors for efficient production.
How much space is required for setting up a production line?
You’ll need enough space for machinery, raw material storage, and vehicle movement, typically around 5,000–10,000 square feet.
Can I automate my concrete block production line?
Yes, automation enhances efficiency, reduces labor costs, and ensures consistency in production quality.
What raw materials are needed for concrete blocks?
Common materials include cement, sand, water, and aggregates like gravel or recycled materials.
How can I ensure sustainability in production?
Use eco-friendly materials, recycle waste, and invest in energy-efficient machinery to minimize your environmental impact.
Is it necessary to test blocks for quality?
Yes, regular testing ensures your blocks meet industry standards for strength and durability, building customer trust.